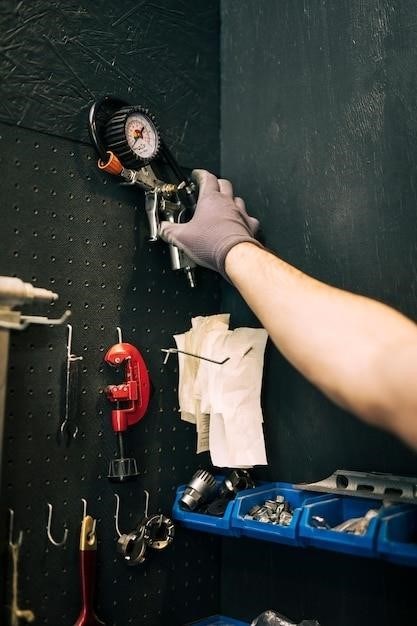
Air Compressor Troubleshooting⁚ A Comprehensive Guide
This guide offers solutions for common air compressor problems. Troubleshooting charts and interactive guides are available online. Consult your owner’s manual for specific repair and service information. Safety precautions are crucial before attempting any repairs.
Identifying Common Air Compressor Problems
A malfunctioning air compressor can stem from various issues. Low air pressure is a frequent complaint, often caused by leaks in hoses, fittings, or the tank itself. Thoroughly inspect all connections for visible damage or loose components. A hissing sound can pinpoint the leak’s location. Another common problem is no air output. This could indicate a faulty pressure switch, a problem with the motor, or a blockage in the air intake. Check the power supply and circuit breakers before inspecting internal components. The compressor might also cycle on and off repeatedly, suggesting a faulty pressure switch or unloader valve. These valves regulate pressure; their malfunction leads to inconsistent pressure and premature wear. Insufficient lubrication is a serious concern. Always check and maintain the correct oil level. Ignoring this can lead to severe motor damage. Lastly, unusual noises like knocking, squealing, or rumbling during operation could point towards issues with the motor or compressor pump, necessitating professional attention. Regularly scheduled maintenance can significantly decrease the frequency of these problems.
Locating Air Leaks⁚ A Step-by-Step Approach
Pinpointing air leaks is crucial for resolving low pressure issues. Begin by turning off and unplugging the compressor for safety. Next, carefully examine all connections, including hoses, fittings, and valves, for visible signs of damage or looseness. A simple visual inspection may reveal cracks or worn seals. If no obvious damage is seen, utilize a soapy water solution. Apply the solution liberally to all connections and joints, watching for bubbling. Bubbles indicate escaping air, precisely locating the leak. Pay close attention to areas under pressure, such as the tank itself and the pressure gauge. Listen attentively for hissing sounds which can be indicative of a leak, especially in hard-to-see places. If the leak is substantial, the sound will be more prominent. Once the leak is identified, repair or replace the damaged component. For minor leaks, tightening connections may suffice. For more significant leaks, replacement parts may be necessary. After repairs, thoroughly retest the system to ensure the leak is completely sealed and pressure is restored to normal levels.
Troubleshooting Low Air Pressure Issues
Low air pressure can stem from various causes, demanding a systematic approach to diagnosis. First, check the air compressor’s tank pressure gauge; a reading significantly below the expected maximum indicates a problem. Inspect the pressure switch; a faulty switch might prevent the compressor from building sufficient pressure. A malfunctioning unloader valve can also cause low pressure by prematurely releasing air. Carefully examine all connections and hoses for leaks; even small leaks can significantly reduce pressure over time. Apply soapy water to connections; bubbles reveal escaping air. The air intake filter might be clogged, restricting airflow and thus pressure. Clean or replace the filter as needed. The compressor pump itself could be failing to generate adequate pressure due to wear or damage. This requires professional assessment and potential repair or replacement. Ensure the compressor’s motor is receiving adequate power; check circuit breakers and fuses. A weak motor will struggle to build pressure effectively. Finally, consider the ambient temperature; extreme temperatures can impact performance, leading to lower pressure output. If the problem persists despite these checks, seek professional assistance for further diagnosis and repair of the air compressor.
Addressing No Air Output from the Compressor
A complete lack of air output from your air compressor points to a more serious issue demanding immediate attention. Begin by verifying the power supply; ensure the compressor is properly plugged in and the circuit breaker hasn’t tripped. Check for blown fuses and replace them if necessary. Inspect the pressure switch; it might be malfunctioning and failing to trigger the compressor. Examine the motor for any signs of damage or overheating; a burnt-out motor requires replacement. Check the air intake for blockages; a clogged filter restricts airflow, preventing air compression. Clean or replace the filter. The unloader valve could be stuck, preventing air from leaving the tank. Inspect and clean or replace the valve if needed. Investigate the compressor pump itself for internal damage; worn seals or broken components necessitate repair or replacement. This often requires professional intervention. Assess the air tank for leaks. A significant leak might prevent pressure buildup. Apply soapy water to all connections and look for bubbles. If the compressor motor runs but produces no air, it suggests a problem within the pump mechanism. Confirm proper lubrication; insufficient oil can damage internal components. Check the oil level and add oil if needed. If all these checks yield no results, a professional air compressor technician will be needed to pinpoint the exact cause of the malfunction and implement the appropriate repair strategy.
Diagnosing and Fixing Pressure Switch Problems
The pressure switch, a crucial component, controls the compressor’s on/off cycle based on tank pressure. A faulty pressure switch can lead to various issues, including continuous running, failure to start, or inconsistent pressure. Begin troubleshooting by visually inspecting the switch for any physical damage, loose wires, or corrosion. Clean any visible dirt or debris. Test the switch’s functionality using a multimeter. Check the switch’s cut-in and cut-out pressures against the manufacturer’s specifications; these values might be found in your owner’s manual or online. Discrepancies often indicate a problem. If the pressure switch consistently fails to activate the compressor, it might be faulty and require replacement. If the compressor runs continuously without shutting off, the cut-out pressure might be misadjusted or the pressure switch is malfunctioning, preventing the compressor from stopping. Similarly, if the compressor fails to start, the cut-in pressure might be incorrectly set. If the switch is difficult to adjust or its contacts appear damaged, replace it. Remember always to disconnect the power before working on the pressure switch. Improper adjustment could lead to compressor damage or safety hazards. If you are uncomfortable working with electrical components or the problem persists, seek professional assistance. A qualified technician can accurately diagnose and fix complex pressure switch problems effectively.
Understanding and Repairing Unloader Valve Issues
The unloader valve is a vital component in an air compressor, responsible for relieving pressure when the compressor reaches its set pressure. A malfunctioning unloader valve can lead to several problems, including the compressor running continuously, overheating, and ultimately, damage to the motor or other components. When the compressor reaches the set pressure, the unloader valve should open, bypassing air back into the intake. This prevents further pressure buildup and allows the motor to rest. If the unloader valve is stuck closed, the compressor will keep running, potentially causing overheating and motor burnout. This condition often results in a continuous cycling or a loud, unusual noise. Start by inspecting the unloader valve for any visible damage, such as cracks, leaks, or debris buildup. Check the valve’s connection points for tightness and ensure that no air leaks are present. Sometimes, a simple cleaning or adjustment of the valve might resolve the issue. If the valve is stuck open, air pressure might not build adequately. This typically results in insufficient air pressure for your applications. If cleaning and adjustment fail, replacement is necessary. Always disconnect the power supply before attempting any repairs to the unloader valve. Remember, improper repair can cause compressor damage and create a safety hazard. If unsure, consult a professional technician for safe and effective repairs.
Maintaining Proper Oil Levels and Lubrication
Consistent lubrication is crucial for the longevity and efficient operation of your air compressor. Insufficient oil leads to increased friction, heat generation, and premature wear of internal components. Regularly check the oil level using the dipstick or sight glass, ensuring it’s within the manufacturer’s recommended range. Use only the type and grade of oil specified in your compressor’s manual; using incorrect oil can damage the compressor’s internal parts. The frequency of oil changes depends on usage and the type of compressor. Consult your owner’s manual for the recommended oil change intervals. During oil changes, inspect the oil for contaminants or unusual discoloration. Dark, gritty, or milky oil indicates potential problems and requires immediate attention. A clogged oil filter can also restrict oil flow, leading to insufficient lubrication. Regularly inspect and change the filter as recommended by the manufacturer. Proper lubrication prevents premature wear on moving parts, reduces the risk of seizing, and ensures consistent performance. Neglecting oil maintenance can lead to costly repairs or complete compressor failure. Always follow safety procedures when handling oil, and dispose of used oil responsibly according to local regulations. Remember, regular oil maintenance is a simple yet highly effective way to maximize the lifespan of your air compressor.
Dealing with Motor and Compressor Repair Needs
Addressing motor and compressor issues often requires professional expertise. If you’ve exhausted basic troubleshooting steps and the problem persists, contacting a qualified technician is recommended. Attempting complex repairs without proper knowledge can lead to further damage or safety hazards. Motor problems can range from simple issues like a tripped breaker or faulty wiring to more complex internal malfunctions requiring specialized tools and diagnostic equipment. Compressor repairs can involve replacing worn seals, damaged piston rings, or other internal components. Locating a reputable repair shop with experience in your specific air compressor model is key. Before undertaking any repairs yourself, always disconnect the power source and follow proper lockout/tagout procedures. Online resources and manufacturer websites may provide diagrams and instructions for simpler repairs, but for major issues, professional help ensures correct diagnosis and repair, minimizing the risk of further damage or injury. Consider factors like cost, reputation, and warranty coverage when selecting a repair service. Regular maintenance, as outlined in the owner’s manual, significantly reduces the likelihood of major motor and compressor failures. Preventative maintenance is far more cost-effective than emergency repairs. Remember safety is paramount; never attempt repairs beyond your skill level.
Safety Precautions During Troubleshooting
Prioritize safety when troubleshooting your air compressor. Always disconnect the power supply before commencing any inspection or repair work. This crucial step prevents electrical shock and injury. Never work on a compressor that is still under pressure; fully depressurize the system before starting any maintenance or repair. Wear appropriate personal protective equipment (PPE), including safety glasses to protect your eyes from flying debris, and gloves to shield your hands from sharp edges or hot surfaces. Be cautious when handling high-pressure air lines and components; sudden pressure releases can cause serious injuries. If you are unsure about any aspect of the troubleshooting process, consult a qualified technician or refer to the manufacturer’s instructions. Proper ventilation is essential, especially when working in confined spaces. Compressed air can contain harmful particles or contaminants, so avoid inhaling it directly. Use caution when handling oil and other fluids; spills should be cleaned immediately to prevent slips and falls. Understand the specific safety warnings and instructions provided in your air compressor’s user manual. Never bypass or disable safety features. If you encounter any unexpected issues or feel uncomfortable at any point during the process, stop and seek professional assistance. Remember, safety is paramount, and taking precautions is crucial to preventing accidents and injuries.
Resources for Further Assistance and Repair
Numerous resources exist for obtaining further assistance with air compressor troubleshooting and repair. Your air compressor’s owner’s manual is an invaluable resource, providing detailed information specific to your model. Online forums and communities dedicated to air compressors offer a platform to connect with experienced users and technicians, sharing advice and troubleshooting tips. Many manufacturers provide dedicated websites with troubleshooting guides, FAQs, and contact information for technical support. Consider contacting a qualified air compressor repair technician for complex issues or when professional assistance is needed. Numerous local businesses specialize in servicing and repairing air compressors, offering expertise and tools unavailable to the average user. Online retailers often sell parts and accessories, making sourcing replacement components easier. Reputable online resources provide comprehensive guides and tutorials, covering various aspects of air compressor maintenance and repair. Educational videos and courses can enhance your understanding of air compressor systems and common problems. Remember to always prioritize safety; if uncertain about a repair procedure, seeking professional guidance is advisable. By utilizing these resources effectively, you can address most air compressor issues successfully and extend the lifespan of your equipment.